Lisans öğrencileri, 1 yüksek lisans öğrencisinden 1 hafta içinde en fazla 2 kelime alacak. 3 kelime almayın aldığınız 3. kelimeden hiç puan alamayacaksınız. Aldığınız kelimeleri yüksek lisans öğrencisinin yayınının altına yazmayın. Dr. Kececi
Saturday, April 30, 2011
Gani Can Öz - 503101305 - 12th Week
2 Utility model
3 Semiconductor
4 Miner's Rule
5 Endurance Limit
6 Wöhler Curve
7 Sun Kink
8 Biofouling
9 Microvoid coalescence (MVC)
10 Dynomometer
Gani Can Öz
503101305
Ozan Kovancı - 11th Week Missing Terms
The master production schedule is a statement of planned future output. It specifies the products(or product options) that will be completed, the time of completion and the quantities to be completed. It is the anticipated build schedule fort he company. As such, it is a statement of production, not a statement of demand. The MPS specifies how product will be supplied to meet future demand. We stess the fact that the MPS is not a forecast, since manufacturing is held responsible for meeting the MPS requirements.
[Manufacturing Planning And Control For Supply Chain Management, Thomas E. Vollmann, William L. Berry, D. Clay Whybark, F. Robert Jacobs, page: 169]
Ozan Kovancı - 12th Week
Armin Bijanzad 12. week
2.Plastic calendering
3.İnjection blow molding
4.Stereolithography
5.3D printing
6.Electrochroming
7.Electroplanting
8.Hot marking
9.Copolymers
10.Sandwich structured composites
Burak Çınar 030060132 12 th week
Belt Conveyor:
This type is available in two common forms: flat belts for pallets, parts or even certain types of bulk materials and troughed belts for bulk materials. Materials are placed on belt surface and travel along the moving pathway. The belt is made into a continuous loop so that half of its length can be used for delivering materials and the other half is the return run (usually empty).
The belt is supported by a frame that has rollers or other supports spaced every few feet. At the each end of the conveyor ( where the belt loops back) are driver rolls (pulleys) that power the belt.
(Computer Aided Design And Manufacturing, Lalit Narayan Et Al., p.529)
Scleroscope:
The Scleroscope test has the distinction of being the first commercially available metallurgical hardness tester produced in the United States. The instrument continues to be used extensively in selected applications.
The test consists of dropping a diamond hammer, which falls inside a galss tube under the force of its own weight from a fixed height, onto the test specimen and reading the rebound travel on a graduated scale. The height of the fall is 250 mm. The hammer is a little less than 6 mm in diameter, 19 mm long, and weights about 2 g. Te shape of the diamond is slightly spherica and blunt with a diameter of approximately 0.5 mm.
(Hardness testing, ASM International, p.91)
Discontinuous Chip(in Metal Machining):
When relatively brittle materials (e.g. cast irons) are machined at low cutting speeds, the chips often form into separate segments ( sometimes the segments are loosely attached). This tends to impart an irregular texture to the machined surface. High tool-chip friction and large feed and depth of cut promote the formation of this chip type.
(Fundamentals of Modern Manufacturing: Materials, Processes, and Systems, Mikell P. Groover, p.491)
Serrated Chips(in Metal Machining):
Serrated chips are semi-continuous in the sense that they possess a saw-tooth appearance that is produced by a cyclical chip formation of alternating high shear strain followed by low shear strain. This fourth type of chip is most closely associated with certain difficult to machine metals such as titanium alloys, nickel base superalloys, and austenitic stainless steels when they are machined at higher cutting speeds. However, the phenomenon is also found with more common work metals (e.g steels) when they are cut at high speed.
(Fundamentals of Modern Manufacturing: Materials, Processes, and Systems, Mikell P. Groover, p.492)
Ertan Toparlak 11th Week Unanswered Terms
11th Week
Polyester glass : It is type of common plastic.Its properties are extremely tough, high dielectric strength, heat resistant, low water absorption, antitracking electrically,self-extinguishing, machinable. Typical uses are insulators and bus braces, switch phase barriers, general electrical insulation, mechanical insulated push rods for switches and breakers, contact blocks, and terminal blocks.
(McGraw-Hill Machining and Metalworking Handbook-3rd Edition-McGraw Hill-Ronald A. Walsh-Chapter 4-P.264)
A. Selim PARLAKYİĞİT - 12th Week
2. Roller Conveyor
3. Belt Conveyor
4. Photodiodes(Type of Photodetectors)
5. Photo transistors(Type of Photodetectors)
6. Robot-Human Charts
7. Discontinuous Chip(in Metal Machining)
8. Continuous Chip(in Metal Machining)
9. Serrated Chips(in Metal Machining)
10.Scleroscope
A. Selim PARLAKYİĞİT - 11th Week Missed Terms
Cutoff is a shearing operation in which blanks are seperated from a sheet metal strip by cutting the opposite sides of the part in sequence, as shown in Figure 20.8(a). With each cut, a new part is produced. The features of a cutoff operation that distinguish it from a conventional shearing operation are the cut edges are not necessarily straight and the blanks can be nested on the strip in such a way that scrap is avoided.
(Fundamentals of Modern Manufacturing, Mikell P. Groover Page 446)
Parting
Parting involves cutting a sheet-metal strip by a punch with two cutting edges that match the opposite sides of the blank , as shown in Figure 20.8(b). This might be required because the part outline has an irregular shape that precludes perfect nesting of the blanks on the strip. Parting is less efficient than cutoff in the sense that it results in some wasted material.
(Fundamentals of Modern Manufacturing, Mikell P. Groover Page 446)

11th week unanswered terms - Gani Can Öz
This popular test (ASTM 3433) is used to obtain the mode I fracture energy of the adhesive bonds, which is a measure of the fracture toughness of the adhesive in the presence of flaws. Similar to a wedge test, a crack is initiated first by inserting a wedge. The specimen is then loaded by pulling apart the two beams at a certain rate, this increasing load resulting in increased deflection of two beams. At a certain critical load, the crack begins to propagate resulting in a slight drop in the load (due to the increased compliance). At this point, the beams are stopped from moving apart, thus keeping the deflection constant. The drop in load (due to increasing crack length) and the crack length are carefully followed. Following the equilibration of the crack, the specimen is consecutively unloaded and then loaded. Ideally, the compliance of the fixture should remain the same during these two cycles if there is no further propagation of the crack. This overall procedure is repeated several times leading to total cleavage of the specimen. The data finally collected at various times consists of load, deflection, crack length and the compliance.
Crystallization, Morphology, Thermal Stability and Adhesive Properties of Novel High Performance Semicrystalline Polyimides Chapter 7: Wedge and Double Cantilever Beam Tests on a High Temperature Melt Processable Polyimide Adhesive, RATTA, VARUN
Friday, April 29, 2011
Osman Süzen 030060804 12 th week
Flexible automation or programmable automation includes:
> Computer- aided design (CAD) - engineering analysis and simulation and computer- aided design and drafting(CADD)
> Computer -aided manufacturing (CAM) consisting of computer numerically controlled (CNC) machine tool, direct numerical control (DNC) machine tool, flexible manufacturing systems (FSM), automated material handlingsystem (AMH) and robotics.
> Computer -aided techniques for management consisting of management information systems (MIS), computer -aided planning (CAP), computer-aided process planning (CAPP),
These tools are used to help design products, manufacture precision products on the factory floor and assist in management of many shop floor ar plant operations. When systems for design, manufacturing and management are used together in a coordinated system, the result is computer -integrated manufacturing (CIM), a new strategy. ( Robotics Technology and Flex - Deb - page 282 )
Induction Heating: Induction heating for forging is now fairly common, particularly for repetitive forging operations. Temperature control for induction heating must be taken seriously, given the rapid heating rates possible with this system. It should be remembered that the temperature of the billet is related directly to its initial temperature and the electrical power input to the induction coil. Commonly, the induction heater is set up the use a specific wattage for a given billet size and weight,based on the billet being at ambient temperature at the outset. The controls downstream of the induction coil can detect a billet temperature outside of the required range and eject the billet from the line. the billet is allowed to cool and is fed back into the system. If the billet is still warm when it enters the coil again, the exit temperature will be higher than intended and the risk of burning is increased. In induction heating lines, optical pyrometer systems are generally used and these must be kept clean and maintained. ( Steel forging: design, production, selection, testing, and application - Edward G. Nisbett - page76 )
Investment casting: In investment casting, the ceramic slurry of a metarial such as colloidal silica ( consisting of nano-sized ceramic particles) coats a wax pattern. After the ceramic hardens(i.e., the colloidal silica dispesion gels), the wax is melted and drained from the ceramic shell, leaving behind a cavity taht is filled with molten metal. The investment casting process, also known as the lost wax process, is best suited for generating most complex shapes. Dentist and jewelers orginally used the precision investment casting process. Currently, this process is used to produce such components as turbine blades, titaniun heads of golf clubs, and parts for kneel and hip prosthesis. In another process known as the lost foam process, polystyrene beads, similar to those used to make coffee cups or packaging materials, are used to produce a foam pattern. ( Essential of materials science and engineering - Donald R. Askeland, Pradeep P. Fulay - page 274 )
Inspection and Testing: Inspection is normally used to examine whether a product conforms to the design standards specified for it. For a mechanical components, this would be probably concerned with the dimensionsi surface texture and tolerances specified for the part. Non-confirming goods result in scrap, rework and the loss of customer goodwill. The common situation that warrant inspection are :
>Incoming materials (raw materials, standard items, subcontracted parts )
>Stage inspection during manufacturing (e.g., when the parts are moved from one production section to another)
>At the completion of processing of the parts
>Before shipping the final assembled product to the customer
Whereas inspection is a regular activity in production, testing is a significant stage of work in product development to prove the capability of the product. Testing is normally associated with the functionalaspect of item, and is often directed at the final product rather than its components. Testing consist of the appraisal of the performance of the final product under actual or simulated conditions. If the product successfully passed the tests, it is deemed suitable for use. Testing ascertains the quality of performance of product. (CAD/CAM/CIM - P.Radhakrishnan - page 493 )
Didem Tarkun(503101304) - 11th week - missing terms
Processing operations are required to transform the starting material into the final form. The operations are performed in the particular sequence required to achieve the geometry and condition defined by the design specification.Processing operations include shaping operations, property-enhancing operations and surface processing operations.Shaping operations alter the geometry of starting work material by various methods. Common shaping processes include casting, forging and machining.Property enhancing operations add value to the material by improving its physical properties without changing its shape.Heat treatment is most common example.Surface processing operations are performed to clean, treat, coat, or deposit material onto the exterial surface of the work. Common examples of coating are plating and painting.
(Groover M.P., Fundamentals of Modern Manufacturing: Materials, Processes and Systems, p. 12)
Didem Tarkun(503101304) - 12th week
2. Flow line production
3. Quantity production
4. Manual work systems
5. Worker machine systems
6. Automated manufacturing systems
7. Flexible automation
8. Closed loop positioning systems
9. Induction heating
10. High frequency resistance heating
Cemre Ablay, 030060150, 12th Week
In dry spinning, the starting polymer is in solution and the solvent can be separated by evaporation. The extrudate is pulled through a heated chamber that removes the solvent; otherwise the sequence is similar to the previous. Fibers of cellulose acetate and acrylic are produced by this process.
(Groover, M.P., Fundamentals of Modern Manufacturing: Materials, Processes, and Systems, 4th Edition, p.285)
...............................................................................................
Wet Spinning:
In wet spinning, the polymer is also in solution-only the solvent is nonvolatile. To separate the polymer, the extrudate must be passed through a liquid chemical that coagulates or precipitates the polymer into coherent strands that are then collected onto bobbins. This method is used to produce rayon (regenerated cellulose fibers.)
(Groover, M.P., Fundamentals of Modern Manufacturing: Materials, Processes, and Systems, 4th Edition, p.285)
...............................................................................................
Planar Coating:
Planar coating is used to coat fabrics, paper, cardboard, and metal foil; these items are major products for some plastics. The important polymers include polyethylene and polypropylene, with lesser applications for nylon, PVC, and polyester. In most cases, the coating is only 0.01 to 0.05 mm (0.0005-0.002 in) thick… In the roll method, the polymer coating material is squeezed against the substrate by means of opposing rolls. In the doctor blade method, a sharp knife edge controls the amount of polymer melt that is coated onto the substrate. In both cases, the coating material is supplied either by a slit-die extrusion process or by calendaring.
(Groover, M.P., Fundamentals of Modern Manufacturing: Materials, Processes, and Systems, 4th Edition, p.285-286)
...............................................................................................
Sandwich Molding:
Sandwich molding involves injection of two separate polymers - one is the outer skin of the part and the other is the inner core, which is typically a polymer foam. A specially designed nozzle controls the flow sequence of the two polymers in the mold. The sequence is designed so that the core polymer is completely surrounded by the skin material inside the mold cavity. The final structure is similar to that of a structural foam molding. However, the molding possesses a smooth surface thus overcoming one of the major shortcomings of the previous process. In addition, it consists of two distinct plastics, each with its own characteristics suited to the application.
(Groover, M.P., Fundamentals of Modern Manufacturing: Materials, Processes, and Systems, 4th Edition, p.294)
Thursday, April 28, 2011
Ertan Toparlak 12th Week
12th Week
1-Trace element method for welding
2-
3-Diffusion Welding (DFW)
4-Thermit Welding (TW)
5-Iterative learning control (ILC)
6-Feedback linearization technique
7-Automatic welding
8-Relative Gain Array (RGA)
9-Multivariable feedback control system
10-Control of arc length (in the welding process)
Ertan TOPARLAK
503091329
İbrahim İLGÜZ 030040113 (12. week)
A rivet is a fastener that has a head and a shank and is made of a deformable material. It is used to join several parts by placing the shank into holes through the several parts and creating another head by upsetting or deforming the projecting shank. During World War II, Rosie the Riveter was a popular cartoon character in the United States. No better image can illustrate the advantages of riveted joints. These are
1. Low cost
2. Fast automatic or repetitive assembly
3. Permanent joints
4. Usable for joints of unlike materials such as metals and plastics
5. Wide range of rivet shapes and materials
6. Large selection of riveting methods, tools, and machines
Riveted joints, however, are not as strong under tension loading as are bolted joints, and the joints may loosen under the action of vibratory tensile or shear forces acting on the members of the joint. Unlike with welded joints, special sealing methods must be used when riveted joints are to resist the leakage of gas or
fluids.
Rivets are made from malleable materials and depend on deformation to fasten and hold components in place. They may be closed either in the red-hot or cold condition depending on the materials to be joined, their thickness and the rivet material. Some techniques for making riveted joints.
(Basic Manufacturing,(Third edition), Roger Timings,p 190)
Electron Beam Welding (EBW)
In EBW process, the heat is generated when the electron beam impinges on work piece. As the high velocity electron beam strikes the surfaces to be welded, their kinetic energy changes to thermal energy and hence causes the workpiece metal to melt and fuse.This process employs an electron gun in which the cathode in form of hot filament of tungsten or tantalum is the source of a stream of electrons. The electrons emitted from filament by thermionic emission are accelerated to a high velocity to the anode because of the large potential difference that exists between them. The potential differences that are used are of the order of 30 kV to 175 kV. The higher the potential difference, higher would be the acceleration. The current levels are low ranging between 50 mA to 1000 mA. The electron beam is focused by a magnetic lens system on the workpieces to be welded. The depth of penetration of the weld depends on the electron speed which in turn is dependent upon the accelerating voltage. When the high velocity electron beam strikes the work-piece all the kinetic energy is converted to heat. As these electrons penetrate the metal, the material that is directly in the path is melted which when solidifies form the joint. Electron beam welding has several advantages which may not be found in other welding processes. The penetration of the beam is high. The depth to width ratios lies between 10:1 to 30:1 can be easily realized with electron beam welding. It is also possible to closely control this penetration by controlling the accelerating voltage, beam current, and beam focus. The process can be used at higher welding speeds typically between 125 and 200 mm/sec. No filler metal or flux needs to be used in this process. The heat liberated is low and also is in a narrow zone, thus the heat affected zone is minimal as well as weld distortions are virtually eliminated. It is possible to carry out the electron beam welding in open atmosphere. For welding in vacuum, the work-piece is enclosed in a box in which the vacuum is created. When electron beam moves in the normal atmosphere, the electrons would be impinging with the gas molecules in the atmosphere and would thus be scattered. This scattering increases the spot size of the electron beam and consequently there is lower penetration. As the vacuum increases, the scattering effect of the electron beam decreases and hence, penetration increases. The other advantage of using vacuum is that the weld metal is not contaminated.
(Introduction to Basic Manufacturing Processes and Workshop Technology,Rajender Singh,p336-337)
Thermit Welding (TW)
It may be of forge or fusion kind of welding. Fusion welding requires no pressure. Thermit welding process is depicted in Fig. 17.29. It is a process which uses a mixture of iron oxide and granular aluminium. This mixture in superheat liquid state is poured around the parts to be joined. The joint is equipped with the refractory mold structure all around. In case of thermit pressure welding, only the heat of thermit reaction is utilized to bring the surface of metal to be welded in plastic state and pressure is the applied to complete the weld. The temperature produced in the thermit reaction is of the order of 3000°C. Thermit welding is used for welding pipes, cables, conductors, shafts, and broken machinery frames, rails and repair of large gear tooth.
(Introduction to Basic Manufacturing Processes and Workshop Technology,Rajender Singh,p335)
Laser Beam Welding (LBW)
Laser beam welding is a fusion welding process. Through the laser beam, the laser produces the energy necessary for welding. It is led to the focusing lens system by mirrors or optical fibers. The lens system then focuses the laser beam on the joint. Depending on the intensity generated there, different processes of beam–material interaction will take place. When the intensity is low, most of the radiation will be reflected by the workpiece, and only a very small part
will be absorbed by the metal in a thin layer (< 1μm) at the surface and transformed into heat. The energy input into the workpiece is achieved by heat conduction.With increasing intensity, the workpiece is locally heated by the laser radiation that is absorbed. When the melting temperature is reached, a molten puddle forms as the time of influence is increased. If the parameters are chosen so as to maintain a stationary state, the process is described as thermal conduction welding.
If, however, the intensity is further increased so that more energy is absorbed than can be dissipated by heat conduction, then the enormous energy density of the laser beam in the focus will cause the metal to vaporize. The pressure of the metal vapor that flows off creates a steam passage in the melt, the so-called keyhole. Typically, the diameter of such a capillary steam tube shows the magnitude of the beam diameter (0.1 to 1 mm). Characteristic threshold intensities for capillary formation lie in the range of 106W/cm2.
In laser beam penetration welding, the system of capillary steam tube and surrounding molten bath is led along the assembly line. The molten bath flows around the capillary on both sides, comes together behind it, and, when solidifying, forms a joint.
(Springer Handbook of Mechanical Engineering, Grote, Antonsson (Eds.),part B, p668-669)
Copolymers
In copolymers the polymer chain is composed of two or more types of monomers. The monomers can be arranged randomly, alternating, or as blocks (short molecule chains, consisting of the same monomer units). Another version is that blocks built from one type of monomer are fixed as side chains onto a backbone built from another monomer type. Common copolymers are polystyrene-butadiene-rubber (SBR) and acrylonitrilebutadiene- styrene (ABS).
(Springer Handbook of Mechanical Engineering, Grote, Antonsson (Eds.),part B, p2079)
Continuous Chip(in Metal Machining)
Continuous chips coming out during machining in machine shop. These types of chips are obtained while machining ductile material such as mild steel and copper. A continuous chip comes from the cutting edge of a cutting tool as a single one piece, and it will remain as one piece unless purposely broken for safety or for convenience in handling. Formation of very lengthy chip is hazardous to the machining process and the machine operators. It may wrap up on the cutting tool, work piece and interrupt in the cutting operation. Thus, it becomes necessary to deform or break long continuous chips into small pieces. It is done by using chip breakers. Chip breaker can be an integral part of the tool design or a separate device.
(Introduction to Basic Manufacturing Processes and Workshop Technology,Rajender Singh,p 402)
Ahmet Gökay Öztürk 030050143 (12thweek)
Although rubber is highly elastic it is not completely so. The best the chemist can achieve is probably represented by the high bounce rubber ball from the toy store, which is a rubber compound with an extremely high proportion of BR ( Polybutadiene Rubber) and a vulcanization system designed for a high state of cure. The chemist can also design a compound, so that a ball made from it hardly bounces at all; toy stores probably have them too. This low bounce ball is said to have a significant viscous component and a low elastic component. This combination of viscous and elastic properties results in the definition of viscoelasticity.
(Andrew Ciesielski, An Introduction to Rubber Technology, pg.127)
Carbon Black
This is a material of major significance to the rubber industry, so it is no surprise that most rubber products we see in the market place are black in color. We have moved a long way from collecting carbon from smokey oil flames, which produced a material called lampblack. The next historical step was to burn natural gas against iron channels, then scrape off the carbon to produce a highly reinforcing material called channel black. Both the use of this black in the rubber industry and its source of supply is currently limited and its cost is somewhat high. There are two common methods of producing carbon black today. Heating natural gas in a silica brick furnace to form hydrogen and carbon, produces a moderately reinforcing material called thermal black. Alternatively, if we incompletely burn heavy petroleum fractions, then furnace blacks are produced. These are the most important blacks in terms of quantity used and available types
(Andrew Ciesielski, An Introduction to Rubber Technology, pg.37-38)
Automated manufacturing systems
Automated manufacturing systems operate in the factory on the physical product. They perform operations such as processing, assembly, inspection, or material handling, in some cases accomplishing more than one of these operations in the same system. They are called automated because they perform their operations with a reduced level of human participation compared with the corresponding manual process. In some highly automated systems, there is virtually no human participation. Examples of automated manufacturing systems include:
• automated machine tools that process parts
• transfer lines that perform a series of machining operations
• automated assembly systems
• manufacturing systems that use industrial robots to perform processing or assernblyoperations
• automatic material handling and storage systems to integrate manufacturing operations
• automatic inspection systems for quality control
Automated manufacturing systems can be classified into three basic types:
(1) fixed automation. (2) programmable automation, and (3) flexible automation.
(Mikell P. Groover, Automation, Production Systems, and Computer-Integrated Manufacturing (2nd Edition)Systems, pg.10)
Closed loop positioning systems
A closed-loop NC system, illustrated in Figure 6.27(h). uses servomotors and feedback
measurements to ensure that the worktable is moved to the desired position. A common
feedback sensor used for NC (and also for industrial robots) is the optical encoder, shown
in Figure 6.28. An optical encoder consists of a light source and a photodetector on either
side of a disk. The disk contains slots uniformly spaced around the outside of its face. These slots allow the light source to shine through and energize the photodetector. The disk is connected, either directly or through a gear box, to a rotating shaft whose angular position and velocity are to be measured. As the shaft rotates, the slots cause the light source to be seen by the photocell as a series of flashes. The flashes are converted into an equal number of electrical pulses. By counting the pulses and computing the frequency of the pulse train, worktable position and velocity can be determined.
(Mikell P. Groover, Automation, Production Systems, and Computer-Integrated Manufacturing (2nd Edition)Systems, pg.183)
Onur OZAYDIN___12th Week
1. Natural Rubber
2. Syntetic Rubber
3. Carbon Black
4. Masterbatch
5. Viscoelasticity
6. Melt Spinning
7. Dry Spinning
8. Wet Spinning
9. Planar Coating
10. Sandwich Molding
Note : All terms are about “RUBBER and PLASTIC TECHNOLOGY”
503101307 Onur OZAYDIN
Doğuş Cendek 030060101 12th Week
Although the nature of the contact , whether it is elastic or plastic,does not affect the true area of contact under the action of a normal load,it may give rise to variations in behaviour when a load is applied which is to the tangetial interface.
(Cherry B.W.,Polymer Surface,p.110)
Stick Slip (28.04 16.10)
The phenemenon of stick slip occurs if there is an intermittent change between static and kinematic friction.It becomes possible,if the dynamical proporties of the ragarded system like elasticity,mass distrubition and damping allow this kind of motion.
(Ulbrich H.,Günthner W., IUTAM symposium on vibration control of nonlinear mechanism and structure,p.223)
Mitering (28.04 16:27)

(Meredith Corp.,123 Quilt,p.15)
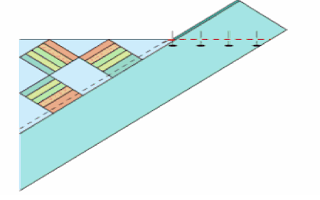
Figure 2
Pinching (28.04 17:15)
Pinching is a useful method of buildings form in clay on any scale and it is frequently used in the studio or classroom as a first experience in clay.Objects both hollow and solid can be made by pinching solid if the cross-section is less than 5cm thick or thicker.If you can fire very slowly as in brick.
(Peterson J.,Peterson S.,The craft and art of clay,p.32)
Ufuk Güneş Civelek 030050161 12th week
Bingham plastic fluids.The Bingham plastic theory assumes that a fluid has a rheology where the relationship between shear stress and shear rate is linear
but the line does not cross the origin of the graph.It looks something like the graph below in figure.
This type of rheology exhibits a yield point.Before the fluid will flow, a certain threshold pressure must be applied and any pressure lower than this will not initiate flow.When the fluid is static, a structure builds up which connects particles in the fluid due to electrostatic attractions between them and forms a gel. For a drilling fluid, this is desirable property because when circulation stops and a gel forms, drilled solids are suspended within the gel and do not sink down through the mud. When sufficient shear stress is applied the fluid starts to move and gel structure breaks down again.The slope of the graph(which a straightline in the mathematical model) is given the term 'plastic viscosity'.Therefore to define the behaviour of a Bingham plastic type fluid,the yield point and plastic viscosity are sufficient to predict the shear stress for a given shear rate.
(Steve Devereux,Drilling for oil & gas: a nontechnical guide,p.157)

Rheology
Rheology is a physical method of charecterization of the structure of matter.Rheology gives unambiguous,physically meaningful,quantative parameters of metarials. These paremeters can be correlated with the structure of matter, either chemical(monecular structure of a compound,length and architecture of a molecule, and so on) or physical (physical intermolecular interactions, phase state, size and distrubution of components in multi-component systems, and so on) structure.Rheological parameters correlate with the structure of material and can be used for structure characterization.
(Aleksandr IAkovlevich Malkin,Alexander Ya Malkin,Avraam I. Isayev,Rheology: concepts, methods & applications,p.351)
Hydrodynamic lubrication
Even in an exclusively hydrodynamic state, the complex physical,hydrodynamic,thermal,elastici and plastic phenomena described in 3.1 exist.Therefore, some hypoteses will have have to be introduced to simplify and permit further treatment of the problem.Two hydrodynamic states can be distinguished:
1.Real hydrodynamic lubrication , in whichall parameters are considered to be interdependent: e.g., variation viscosity with pressure, temperature,and velocity gradien; heat transfer; roughness and deformations.
2. Ideal hydrodynamic lubrication, in which viscosity is constant in time and space; surfaces are perfectly smooth, rigid and without deformations;and thermal equilibrium is established.Further external forces and velocities are often considered to be constant in time.
(Nicolae Tipei,Theory of lubrication: with applications to liquid- and gas-film lubrication, p.39)
Elastohydrodynamic lubrication
The term elastohydrodynamic lubrication (EHL) is reserved for hydrodynamic lubrication applied to lubricantfilms between elastically deforming solids.The principles of EHL are readily applicable to such diverse objects as gears, rolling-element bearings, and human animal joints. In general bearingsthat are lubricated in EHL mode are of low geometric conformity, and, in the absence of lubricant film and of elastic deformation, the opposing surfaces would contact in a point (ball bearings) or along a line (gears or roller bearings).
If the solid surfaces that are lubricated in the EHL mode have large elastic modulus,the contact pressures will be largei perhaps of the order of 1GPa.The film thickness will be correspondingly small, of the order of 1μm. Under such conditions the material properties of the lubricant will be distinctly different from its properties in bulk.This change in lubricant properties, when coupled with the effects of elastic deformation of the solid surfaces, yields film thicknesses one or two orders of magnitude larger than those estimated from constant viscosity theory applied to nondeforming surfaces.
EHL theory may be viewed as a combination of hydrodynamic lubrication, allowance for the pressure dependence of viscosity, and elatic deformation of bounding surfaces.
(Andras Z. Szeri,Fluid Film Lubrication,p.37)
Eray Çavuş 030060022 12th week
Graphite is used in making moulds to receive alloys such as titanium, which can be poured only into inert moulds. The casting process must be performed in a vaccum to eliminate aany possibility of contaminating the metal. The graphite moulds can be made either by machining a block of graphite to create the desired mould cavityor by compacting a graphite base aggregate around the pattern and then sintering the obtained mould at a temperature 1800 to 2000 F in reducing atmosphere. In fact, graphite mould liners have found widespread industrial applications in the centrifugal casting of brass and bronze.
(Product design and manufacturing, Yazar: A.K. Chitale, R.C. Gupta, Page 93)
Natural Rubber (28,04 20,25)
Natural rubber occurs as a latex that may be tapped or removed from the rubber bearing plant or tree. The latex is subsequently coagulated and the precipitated material collected. Originally, natural rubber was harvested in its wild state from South America, especially from Hevea brasileanus trees. The Hevea tree is not a unique source of rubber. Mant other plants from the South American regions produce rubbery as well as plastic materials. It is very possible that the hull balls obtained by Columbus and the conQuistadors did not derive from Hevea. Most efforts toward commercially producing natural rubber from other plants have focused on the Guayule bushes of the Mexican desert.
(Rubber processing: technology, materials, principles, Yazar: James lindsay White)
Syntetic Rubber (Synthetic Rubber) (28,04 20,43)
Today, the tonnage of synthetic rubbers is more than three times that of natural rubber. Development of these synthetic materials was motivated largely by the world wars when NR was difficult to obtain. The most important of the synthetics is styrene-butadiene rubber (SBR), a copolymer of butadiene and styrene. As with most other polymers, the predominant raw material fofr the synthetic rubbers is petroleum. Only the synthetic rubbers of greatest commercial importance are discussed here. Market share data are for total volume of natural and synthetic rubbers. About 10% of total volume of rubber production is reclaimed; thus, total tonnages do not sum to 100%.
(Fundamentals of Modern Manufacturing: Materials, Processes, and Systems, Yazar: Mikell P. Groover, Page 178-179)
Feedback Linearization Technique
Most physical systems operations are nonlinear in nature and hence they should be described by means of nonlinear mathematical models. Since nonlinear models are not convenient for control purposes, due to both theoretical and computational reasons, they are often linearized by using appropriate exact or approximate linearization techniques. Among them, feedback linearization control law and a state variable transformation (diffeomorphism) such that the closed loop system model becomes linear, in the new coordinate variables. However, feedback linearization requires some strong constraints to be satisfied by the original nonlinear system, and thus its applicability is quite restricted. If, in addition, the original system is characterized by uncertain parameters, external disturbances and unmeasured state variables, as is the case of bioprocess control systems, the linearization problem becomes particularşy complex and almost inextricable.
(Proceedings of the International Conference of Computational Methods in Sciences and Engineering 2003 (ICCMSE 2003),Yazar:T.E. Simos, Page 90)
Elif Naz Aladağ, 030060027, 12th Week
- Polymer as carrier
- Colorants
- Dispersing agent
- If necessary; additives such as stabilizers, nucleating agents, antisatic agents, lubrications, and so forth
Sezgin Koçak-030070026-12th Week
Tribocorrosion is an irreversible transformation of a material resulting from simultaneous physicochemical and mechanical surface interactions taking place in a tribological contact. Tribocorrosion involves numerous synergy effects between mechanical and chemical or electrochemical phenomena including corrosion accelerated occurs in many types of contacts such as sliding contacts, rolling contacts, fluid or particle impingement, as well as erosion and abrasion phenomena in fluids due to suspended particles. Technical systems of sliding contact in aqueous media are found for example in pumps, mining equipment, medical implants, metal grinding. Fretting corrosion is a particular case of tribocorrosion of solid-solid contacts resulting from low amplitude oscillations in a corrosive environment.
(Edited By: S. Virtanen, P. Schmuki, G.S. Frankel, Critical Factors in Localized Corrosion IV, p. 618)
Elastomer Friction:
Elastomers are usually formulated to have high friction coefficients against a wide variety of counterfaces but the friction coefficients can be very low in some cases. Table 4 shows friction coefficients for some common elastomers against hardened stainless steel; the coefficients are quite high. On the other hand, in water, the coefficient of polyurethane against most other solids is less than 0.2. The slippery nature of this elastomer became apparent when these materials came into vogue in the 70’s for floor finishes. They produced a very abrasion resistant surface, but when wet they were a safety hazard. Their use as tires and floor toppings has almost ceased but they are now used for seals and wear parts in pumps where their slipperiness and abrasion resistance have a synergistic effect.
The coefficient of friction of many elastomers against other solids is often 1 or more, but the use environment may significantly alter the friction characteristics.
(K. C. Ludema,Raymond George Bayer,ASTM Committee G-2 on Erosion and Wear,Tribological modeling for mechanical designers, p.113)
Ultrasonic Transducer:
The mechanical construction of a typical ultrasonic transducer used in contact testing is shown in Fig. 1.7. A very thin (app. 100µm thick) piezoelectric crystal is plated on both faces; it is attached through a small electrical network contained in the transducer housing to the external BNC or microdot of the transducer. Since the crystal is very fragile, a ceramic wear plate protects the front face of the crystal, as shown. The back face of the crystal is attached to a layer of epoxy loaded with tungsten particles. This backing acts as a highly attenuating medium that controls the shape and duration of the pulse.
There are actually two types of contact transducers. They are distinguished by the types of motion generated in the crystal when excited by a voltage pulse and the corresponding types of motion subsequently present in the ultrasound beam launched from the transducer into the part. Figure 1.8(a) shows a contact P-wave transducer with the crystal excited in a mode that causes its thickness to expand and contract normal to the surface, thereby producing a wave with similar motions that is called a P-(pressure) wave. Figure 1.8(b) in contrast shows S-wave transducer with the crystal excited in a shearing type of motion, thereby producing an S-wave (shear) wave.
(Lester W. Schmerr, Fundamentals of ultrasonic nondestructive evaluation: a modeling approach, p.6)